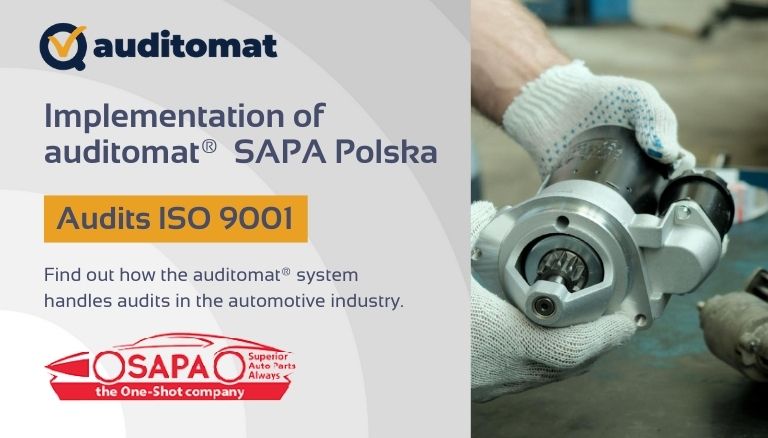
The aim of the GoStandard project is to develop a transparent, user-friendly and fully digital, cloud-based IT solution for monitoring the performance of standardized work, based on the implementation of electronic checklists and routine audits in all functional areas of the company. The assumption of the project is to achieve high accessibility and universality of the system, both in terms of employee engagement and satisfaction, as well as fast and efficient information flow.
The main challenge addressed by the project, as defined in ASAP #1 action, is to implement a system for monitoring the execution of standardized work within the Organization. Taking on this challenge has been prioritized for implementation due to its potential for delivering significant benefits with relatively low associated costs. Without continuous monitoring and improvement of the process, its sustainable maintenance over time becomes unattainable, resulting in destabilization and hindering the achievement of expected process outcomes. This challenge is directly linked to the necessity of aligning business processes with sustainable development, particularly impacting the enhancement of knowledge/information management and employee communication, thus improving mobility. The indirect challenge of implementing a work standardization monitoring system is to achieve a high level of its accessibility and universality – to involve in the process as many employees as possible. This challenge is described in #3 ASAP action as employee training process to fulfill skill gaps.
As first part of the project, action #1 was implemented, as defined in the developed ASAP – “Definition and customization of business processes for communication and mobility”. Firstly, a comprehensive analysis of the entire business process within standardized work was conducted, along with the identification of stakeholders’ needs. This facilitated the development of guidelines for the pilot implementation of an electronic system to support and monitor the execution of standardized work. The solution is based on a cloud-based system – the auditomat® web application. Within the project, the system was customized and appropriately configured to serve as a central, stable, and user-friendly electronic system.
Following the suggestion in Task 3, a series of courses was conducted in with 70 percent of employees participated. As part of the pilot tests, they easily completed the defined electronic checklists and audits using a web-based application without having to perform redundant tasks such as printing forms, processing photos, preparing reports, and distributing results – the entire process has been automated. As a result, communication and information circulation have been improved – by making data available in real-time from anywhere. Additionally, the system is based on centralized data, enabling multi-level statistical analysis and ultimately facilitating accurate and swift business decisions. This will directly contribute to improving work safety and enhancing competitiveness. The predictability of the process will serve as a factor stimulating an increase in the quality of production.
The main result of the project was a pilot test in which 70% of employees were involved. As part of the tests, 936 electronic checklists and audits were completed and 14 employee suggestions were made.
As a result of the twice performed research based on the Q12® survey developed by the Gallup Institute, it was shown that the introduction of an electronic system for monitoring standardized work had a positive impact on employees. The overall level of job satisfaction among all employee groups increased by more than 20%