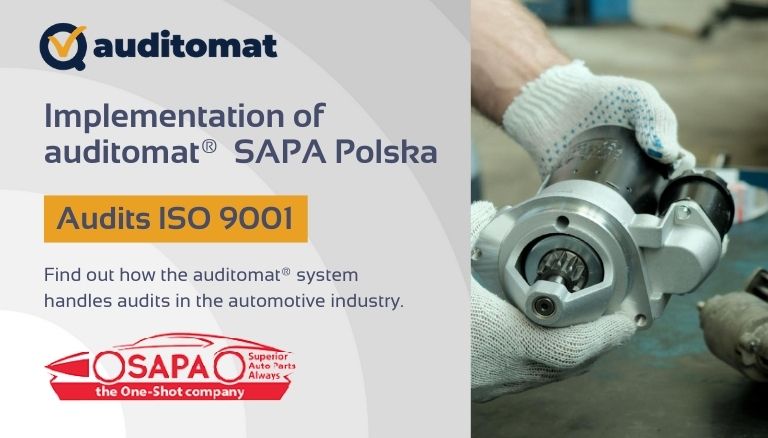
Whether it was short talks during breaks at conferences, individual presentations, or long-term implementations, each meeting, each person was an opportunity for me to gain new knowledge and valuable experience.
I have also always believed that the only source of inspiration shaping the direction of auditomat development should be the reality of our users. Only by focusing on the day-to-day challenges of continuous improvement processes, standardization and its monitoring can we deliver a solution that effectively improves their quality, safety and efficiency. It is not uncommon for seemingly minor and insignificant process obstacles to have a butterfly effect, significantly shaping the results (or lack thereof).
Let’s start with the title “IT” – what is it really? Depending on who you ask in a particular organization – be it a production manager, lean manager, quality or occupational safety specialist – you will get similar, but nonetheless slightly different answers. In addition, these answers will be determined by the specifics of the industry, others in automotive, others in window manufacturing, furniture or large-format printing. Going beyond the manufacturing sector would yield entirely new terms. The owner of a store or restaurant would use different language than the director of a chain of car dealerships or another service outlet.
But what if we asked the same people to avoid using specific names of proprietary methodologies, tools or practices used in a given environment, industry or corporation? The resulting descriptive representation of our ‘IT’ would turn out to be very similar.
In each case, the priority is to effectively monitor the repetition and pattern of activities in order to identify and analyze deviations and problems. This, in turn, provides an opportunity to take corrective and improvement actions. In other words, we are talking about the Standardization Monitoring Process – crucial for effective operation in any business area.
It can be said that everything is subject to standardization: processes, work patterns, job organization, covering aspects such as safety, fire protection, quality assurance or repeatable behavior. Whether we are talking about Lean philosophy, health and safety rules, product quality control, or even the procedure for opening a restaurant or salon – the process of monitoring standardization in the broadest sense, regardless of the name used, the context, the source of origin or the level of formalization (it can even be based on the experience of employees) is always the same process.
Our experience in the field of diverse industries has enabled us to separate the processes of monitoring standardization and continuous improvement from the internal and external factors affecting each organization. The knowledge we gained allowed us to look at the process from a broader perspective, which made it possible to precisely identify the key and most recurring difficulties, which in many cases are underestimated.
Professional training, workshops for employees, certified knowledge and extensive experience of the staff – all this is essential for smooth operation and effective adaptation to changing conditions, both internal and external, in the specific environment of each organization. The use of proven methods, implementation of tools and adherence to industry best practices, is an important component of further development.
However, I would like to draw attention to an aspect that is often overlooked – the process of monitoring the functioning of the introduced standards, schemes, as well as their effectiveness.
I will use an example from the field of workstation organization according to the Lean philosophy. We are implementing 5S. Without going into the details of the 5S implementation process itself, we go through all the “S’s” one by one, using the knowledge gained in training, introducing various good practices to effectively organize the workstation. One of the elements of implementing 5S is conducting 5S audits. We develop checklist schemes and an audit schedule, determining with what regularity the positions will be checked and by whom.
And please note – the main focus here is on methodology. Should we use a ready-made audit list template, or create our own? Are 0/1 type questions better, or is a point scale more appropriate? How should we analyze the results? Should we create a dedicated group of 5S auditors, or involve every employee? Should we schedule audits once a week, or perhaps once a month?
When an attempt to implement 5S does not bring the desired results, we often decide to change the approach, replacing it, for example, with a proprietary method such as the standard “ensuring cleanliness at the workplace”, with the implementation of “cleanliness audits”. Unfortunately, such a change often does not bring the desired results, because the problem, as a rule, lies not in the methods themselves, but in the daily activities of the monitoring process. It is this process that lays the foundation for further improvement of our standards and makes it possible to maintain their continuity.
Of course, this does not mean that methods are unimportant – absolutely not. However, it is equally important to maintain balance, equilibrium and pay attention to the way the monitoring process is carried out, i.e. the daily routine. In this way, those involved in the process not only monitor whether other processes are optimal, effective and efficient, identifying even the smallest hindering factors, but also move within the optimal environment and pattern of their work. As a result, they don’t have to face problems on a daily basis, which promotes efficient and smooth execution of tasks.
In practice, we often encounter very inefficient and chaotic monitoring processes that contain a huge number of regularly repeated unnecessary activities. Even when they belong to the “Lean world” – for example, it happens in 5S audits that a large part of the process does not bring any value, especially from the customer’s perspective. Significant room for improvement is also left by an important and crucial aspect – the speed and completeness of information flow. We will discuss these problems and their effects in detail in the following sections of our academy.
If we neglect the optimization aspect of the monitoring process, leaving in place a series of difficulties, waste and delays in the flow of information that at first glance may not seem important from the perspective of the whole enterprise, over time we may find that we cause a butterfly effect. Small, day-to-day activities that are merely elements of an auxiliary process can ultimately lead to the ineffectiveness of even the most carefully implemented tools, methods and practices – that is, standardization.
It is worth noting that standardization is an ongoing process, and our cyclical goal is to strive for excellence, not a one-time implementation of a tool. The lack of an effective and optimally functioning monitoring process makes it impossible to maintain continuous improvement and dynamically adapt standards to changing realities. It is a matter of time when our standards will no longer be the most optimal scheme, and their strict adherence will negatively affect the efficiency of operations.
Returning to the 5S example, implementing this approach is not a one-time “tidying up” of a workstation, but the adoption of a methodology, principles and criteria by which we organize the workstation. The goal is to keep the positions always in the most optimal configuration, adapted to the work being performed. The monitoring system plays a key role here as a mechanism for signaling the need for change. However, while it is often the weakest, inflexible and overlooked element of standardization, it only provides information on compliance with previously established rules, which may prove ineffective and inadequate at the present time.
In practice, this not only leads to an obvious departure from the stated principles, but also builds a strong belief among employees in the futility of implementing them and generates resistance to engaging in the process, which often results in a reluctance to make further “improvements” in the future.
This concludes the first episode of the Optimal Audit Academy. In the following sections, I will provide specific examples of the problems and waste we most often encounter when analyzing standards monitoring processes, while pointing out the consequences of their occurrence.